
List formed using information from īradken, Inc. Table 1 – Top metal casting companies in the USA Additional details about each company are included such as headquarters location, number of employees, and brief company summaries. Table 1 contains relevant information on the top metal casting companies in the USA, ranked by annual sales in USD.

Top Metal Casting Companies in the USA on There are hundreds of casting companies in the market, but this article will detail today’s top U.S. These contract services allow parts procurement without the weighty overhead costs of in-house casting equipment, space, and workers. produce 10,000 parts, perform casting for a year, etc.). Some casting companies will pair with buyers to manufacture parts for them under a contract basis (i.e.
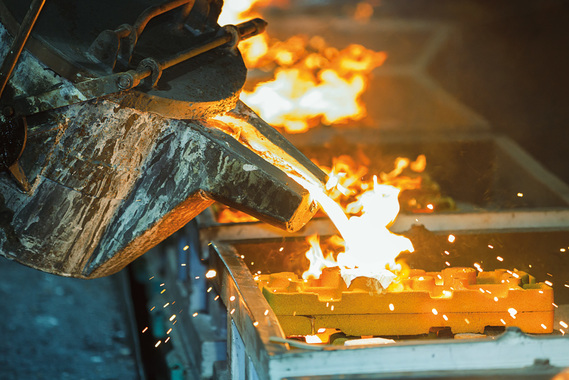
Casting companies have specialized equipment to perform specific techniques such as investment casting, die casting, sand casting, etc., often with built-in automation and control. What is a casting company, and what do they do?Ī casting company performs casting procedures on steel and other metals (such as foundries) and/or sells and distributes cast parts for buyers. To learn about this metal fabrication technique and its modern implementations, read our article about the types of casting processes. From raw materials to intricate assemblies, casting is an invaluable additive process that reduces the need for difficult machining and other subtractive methods. Since then, casting has become the foremost tool used by manufacturers to create highly complex, homogenous, and replicable metal products. Casting has been used for thousands of years, where ancient people would cast brass, iron, copper, and other metals into jewelry, weaponry, and more. Waupaca Foundry was awarded the “Best Casting Conversion” for a rear suspension trailing arm.Image credit: Funtay/ What is Casting?Ĭasting is a manufacturing process where molten, liquid metal is poured into a mold and is left to cool to conform to the mold’s shape when solidified. Matched with front suspension arms, the result is a smoother ride, more consistent tire contact, and increased hillside stability for the consumer. The rear suspension features a cast 3-link trailing arm-the first and only of its kind in the industry. Bad Boy Mowers recognized the improvements the casting would have on its operations and approved tooling to start on the project. As a proactive measure, assembly models were used to compare the 8-piece weldment to the single ductile iron casting prior to production. Tooling engineering at Waupaca Foundry led the design of the casting. The company realized that converting the weldment to a casting improved the overall quality, reduced warranty costs, and improved assembly.

However, the fabricated weldment’s strength did not withstand impact testing, and with the many components of the weldment, the fit was never perfect, resulting in gaps. While a change in the makeup of a part may be intimidating, the product design to just one single part emphasizes iron castings and the production complexities it can eliminate.īad Boy Mowers was looking to improve the quality and durability of the eight-piece steel weldment, rear suspension trailing arm on their Commercial Zero-Turn Mower, fabricated internally. American Foundry Society Awarded Waupaca Foundry "Best Casting Conversion."Įliminated Bad Boy Mowers’ current strength issues and exceeded their quality expectations.
